-
Titanium Pipe Fittings
-
Titanium Welded Pipe
-
Titanium Pipe Flange
-
Seamless Titanium Tubing
-
Titanium Heat Exchanger
-
Titanium Coil Tubing
-
Titanium Alloy Sheet
-
Titanium Fasteners
-
Titanium Welding Wire
-
Titanium Round Bar
-
Titanium Forgings
-
Titanium Clad Copper
-
Titanium Electrode
-
Metal Sputtering Target
-
Zirconium Products
-
Sintered Porous Filter
-
Shape Memory Nitinol Wire
-
Niobium Products
-
Tungsten Products
-
Molybdenum Products
-
Tantalum Products
-
Equipment Products
-
Aluminum Products
-
Stainless Steel Products
BT9 Titanium Bar Metal 50% Lighter Than Steel For Aerospace Engines
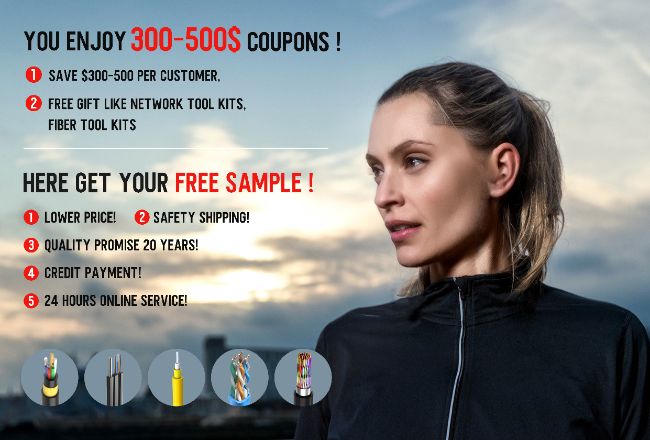
Contact me for free samples and coupons.
Whatsapp:0086 18588475571
Wechat: 0086 18588475571
Skype: sales10@aixton.com
If you have any concern, we provide 24-hour online help.
xMaterial Grade | BT9 | Heat Treatment | Optional, Based On Application |
---|---|---|---|
Dimention | As Order | Feature | High Special Strength |
Processing Equipment | CNC Lathe, Hydraulic Press, Rolling Mill | Weight | Actual Weight |
Length | Customizable | Materials | Titanium |
Yield Strength | 880-980 MPa | Sample | Avaliable |
Highlight | Metal Titanium Bar,Metal BT9 Titanium Bar,Aerospace Engines BT9 Titanium Bar |
BT9 Titanium Bar Metal 50% lighter than steel For Aerospace Engines
Composition: Ti-6.5Al-3.5Mo -1.5Zr-0.3Si
tensile strength: 900-1100 MPa.
yield strength: 880-980 MPa.
Elongation: 10% ~15%.
Hardness: HB290-320.
What Is Titanium Bar Metal?
Titanium Bar Metal exhibits remarkable properties when compared to other materials such as steel and aluminum. Here is a summary of its characteristics:
- Lightweight Yet Strong: Titanium is nearly 50% lighter than steel, which makes it highly desirable in applications where weight is a critical factor. Despite its lightness, titanium boasts a strength that is 30% greater than steel, making it exceptionally strong for its weight.
- Greater Durability: Even though titanium is 60% heavier than aluminum, it offers double the strength, which underscores its superior durability and resistance to mechanical stresses.
- High-Temperature Resistance: Titanium maintains its structural integrity and strength up to temperatures of 1,000 degrees Fahrenheit (537 degrees Celsius). This high-temperature resistance makes it suitable for applications in extreme heat conditions.
- Alloyed for Enhanced Properties: To further improve its strength, high-temperature performance, and to make the material more workable, titanium metal is alloyed with other elements such as aluminum, manganese, iron, molybdenum, and others. These alloying additions enhance the composite's overall properties while maintaining titanium's inherent benefits.
- Corrosion Resistance: One of titanium's outstanding features is its high resistance to corrosion. When exposed to air, titanium forms a tight, stable oxide film on its surface. This passive layer protects against various corrosive agents, particularly saltwater, which is crucial for marine applications and other environments where corrosion could be a significant issue.
In summary, the combination of titanium's lightweight nature, high strength, ability to maintain its properties at elevated temperatures, and exceptional corrosion resistance makes it an extremely valuable material across numerous sectors, including aerospace, automotive, marine, medical, and many others where these traits are highly sought after.
The properties of Titanium Metal Bar make it a material of choice for various critical applications, particularly in the aerospace industry. Here's an overview of its characteristics and uses:
1. High Specific Strength: This refers to the strength of the material relative to its density, making titanium metal both strong and lightweight. This is especially important in applications where weight is a crucial factor, such as in aircraft design.
2. Mid-Temperature Performance: Titanium maintains good mechanical properties at moderate temperatures. It can be used effectively up to 500°C, which allows it to be applied in environments that may experience moderate heat without sacrificing performance.
3. Corrosion Resistance: Titanium has excellent corrosion resistance due to the formation of a protective oxide film on its surface when exposed to air. This makes it suitable for use in environments where many other materials would corrode quickly, such as marine conditions or harsh chemical environments.
4. Lightweight: As previously mentioned, being nearly 50% lighter than steel, titanium reduces the overall mass of structures, which is vital for vehicles requiring high maneuverability and those designed for maximum fuel efficiency.
5. High Yield and Fatigue Strength: The yield strength indicates the point at which a material will begin to plastically deform under stress, while fatigue strength relates to its ability to resist failure under repeated loading and unloading. Titanium's high values for both are particularly beneficial in applications involving repeated stresses, such as aircraft flight operations.
Titanium Metal Bar is notably used in several key components of aero-engines, including:
- Compressor Discs: These require materials that can withstand high forces and temperatures without deformation or failure.
- Turbine Discs: Similarly, these components operate in extreme conditions and need materials that maintain their integrity under stress and heat.
- Casings: Lightweight yet strong casings are essential for engine performance and safety.
- Compressor Blades: These must be able to handle the forces of rotating masses of air, requiring high strength and fatigue resistance.
- Fasteners: Titanium’s high strength and corrosion resistance make it ideal for securing critical components in a high-stress environment.
Given its properties, Titanium Metal Bar is not only ideal for aerospace engine parts but has also found widespread use in the aviation industry, as well as in sectors like energy, chemicals, and others where high strength, lightweight construction, and corrosion resistance are paramount.
Specification
Chemical Composition Wt%
Al | Mo | Zr | Si | Fe | C | N | H | O | |||||||
5.8~7.0 | 2.8~3.8 | 0.8~2.0 | 0.2~0.35 | ≤0.25 | ≤0.08 | ≤0.05 | ≤0.012 | ≤0.15 | |||||||
Smelting method | |||||||||||||||
Electrode pressing + three times of vacuum self-consumption | |||||||||||||||
Mechanical properties (Φ28 rolled bar longitudinal) | |||||||||||||||
Heat treatment system:950℃´1h;cold+ 530℃´6h; cold. | |||||||||||||||
Room Temperature(20℃) | σb MPa | σ0.2 MPa | A % | Z % | Ak J | HBd | |||||||||
1133 | 1054 | 16.0 | 46 | 49 | 3.3 | ||||||||||
1138 | 1065 | 18.0 | 50 | 44.3 | 3.34 | ||||||||||
High temperature(500℃) | 795 | — | 20 | 66 |
σ(640 ) MPa ³35h |
Qualified | |||||||||
795 | — | 20 | 65.5 | Qualified | |||||||||||
500℃´100h Heat exposure |
1136 | 1078 | 17.0 | 47.0 | — | — | |||||||||
1125 | 1063 | 16.5 | 46.0 | — | — |
Inspection items
Destructive testing: physical performance testing, hardness testing, chemical composition testing.
Non-destructive testing: ultrasonic testing, penetration testing, appearance testing.
Titanium and its alloys play a pivotal role in the aerospace industry, particularly in engine components, due to their exceptional combination of properties. Here's an overview of why they are so essential:
1. **High Strength and Low Density**: A critical factor in aerospace engineering is the strength-to-weight ratio. Titanium's high strength coupled with its low density makes it ideal for reducing weight without compromising on load-bearing capabilities. This directly contributes to improved fuel efficiency and performance.
2. **Heat and Stress Resistance**: Aerospace engines operate under extreme conditions of heat and mechanical stress. Titanium alloys like BT9 and TC11 are specifically developed to maintain their integrity at the high temperatures and pressures found within these engines, making them indispensable for creating durable engine components.
3. **Fatigue Resistance**: Repeated cycles of stress and unstress are common in aircraft components during flight operations. Titanium alloys provide excellent fatigue resistance, ensuring that the materials can handle the cyclic loading without failing.
4. **Corrosion Resistance**: The ability of titanium to resist corrosion is another key factor in its widespread use in aerospace applications. The natural oxide layer that forms on its surface when exposed to air acts as a protective barrier against corrosive elements, extending the life of engine components and reducing maintenance costs.
The production process for titanium bars used in aerospace engines is sophisticated and precise. Advanced techniques such as precision forging or hot isostatic pressing (HIP) are employed to create high-quality, defect-free material. These processes ensure that the metal's grain structure is optimized for strength and durability. Further processing steps like machining or heat treatment may follow to achieve the exact specifications required for each component.
In summary, titanium bar metal is a crucial material for aerospace engine applications due to its high strength, low density, and excellent corrosion resistance. It is integral in various components, including compressor blades, turbine discs, and engine casings, playing a vital role in ensuring the safe and efficient operation of modern aircraft.