-
Titanium Pipe Fittings
-
Titanium Welded Pipe
-
Titanium Pipe Flange
-
Seamless Titanium Tubing
-
Titanium Heat Exchanger
-
Titanium Coil Tubing
-
Titanium Alloy Sheet
-
Titanium Fasteners
-
Titanium Welding Wire
-
Titanium Round Bar
-
Titanium Forgings
-
Titanium Clad Copper
-
Titanium Electrode
-
Metal Sputtering Target
-
Zirconium Products
-
Sintered Porous Filter
-
Shape Memory Nitinol Wire
-
Niobium Products
-
Tungsten Products
-
Molybdenum Products
-
Tantalum Products
-
Equipment Products
-
Aluminum Products
-
Stainless Steel Products
ASME SB338 Titanium Tube Seamless and Welded for Heat Exchangers
Place of Origin | CHINA |
---|---|
Brand Name | CHANGSHENG |
Certification | ISO9000:2015 |
Model Number | GR1 GR2 GR3 GR7 GR12 |
Minimum Order Quantity | 20KG |
Price | According to quantity |
Packaging Details | Clients’ requirement |
Delivery Time | 10 working days |
Payment Terms | T/T, Western Union, MoneyGram |
Supply Ability | 300 tons per month |
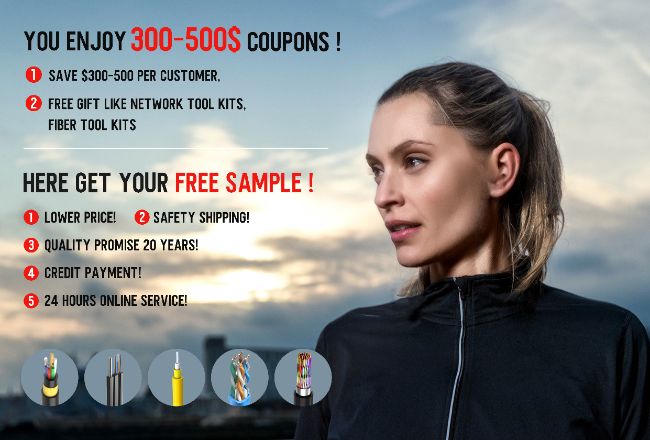
Contact me for free samples and coupons.
Whatsapp:0086 18588475571
Wechat: 0086 18588475571
Skype: sales10@aixton.com
If you have any concern, we provide 24-hour online help.
xTube Shape | Round Tube | Oem | We Can Offer As Your Drawing |
---|---|---|---|
Standard | ASTM B338/ASME SB338 | Surface Process | Polished, Pickled, Passivated, Etc. |
Dimensions | Can Be Customized | Size | Customizable |
Shape | Round | Grade | Gr1, Gr2, Gr3, Gr7, Gr12 |
Highlight | Welded ASME SB338 Titanium Tube,Heat Exchangers ASME SB338 Titanium Tube,Seamless ASME SB338 Titanium Tube |
ASME SB338 Titanium Tube Seamless and Welded for Heat Exchangers
Introduction
The ASTM B338 is a designated standard for both seamless and welded titanium and titanium alloy tubes used in applications like condensers and heat exchangers. This standard outlines the specifications and requirements for 22 different grades of titanium tubing, primarily intended for use in surface condensers, evaporators, and heat exchangers.
The scope of the ASTM B338 titanium tube standard encompasses a wide range in terms of size, type, wall thickness, shape, and length to accommodate the diverse needs of various industries. Here's a detailed breakdown:
- Size: The standard caters to tubes with diameters ranging from 6mm up to 610mm, offering flexibility for different scales of engineering solutions.
- Type: It includes various types of manufacturing processes for tubing, such as seamless (which is made without any seam or weld), electric resistance welded (ERW), welded, and fabricated tubes, ensuring that the right type of tube can be selected based on specific application requirements.
- Wall Thickness: The minimum wall thickness should be 0.5mm or greater, ensuring adequate strength and durability for the tubes in their intended service.
- Shape: While round tubes are the most common, the standard also includes options for square and rectangular shaped tubes, allowing for specialized uses where these geometric shapes are necessary.
- Length: The standard offers flexibility in length with single random length, double random length, or custom lengths based on the customer's actual request, up to a maximum length of 12000mm, providing considerable adaptability for project requirements.
In summary, the ASTM B338 titanium tube standard provides a comprehensive guideline for the production and application of titanium tubes in various forms and sizes, ensuring they meet the necessary standards for performance in condensers and heat exchangers across multiple industries.
Titanium Tube Chemical Composition:
Element | Composition % | |||||
Grade 1 | Grade 2 | Grade 3 | Grade 7 | Grade 9 | Grade 12 | |
Nitrogen, max | 0.03 | 0.03 | 0.05 | 0.03 | 0.03 | 0.03 |
Carbon, max | 0.08 | 0.08 | 0.08 | 0.08 | 0.08 | 0.08 |
Hydrogen, max | 0.015 | 0.015 | 0.015 | 0.015 | 0.015 | 0.015 |
Iron, max | 0.2 | 0.3 | 0.3 | 0.3 | 0.25 | 0.30 |
Oxygen, max | 0.18 | 0.25 | 0.35 | 0.25 | 0.15 | 0.25 |
Aluminum | … | 2.5-3.5 | Mo(0.2~0.4) | |||
Vanadium | … | 2.0-3.0 | Ni(0.6~0.9) | |||
Palladium | … | 0.12-0.25 | ||||
Residuals, max each | 0.1 | 0.1 | 0.1 | 0.1 | 0.1 | 0.1 |
Residuals, max total | 0.4 | 0.4 | 0.4 | 0.4 | 0.4 | 0.4 |
Titanium | balance | balance | balance | balance | balance | balance |
Application
Titanium tubes are precision-cut to order, tailored to meet the specific requirements of various applications due to their exceptional properties. These tubes are known for their high strength and low density, making them ideal for situations where weight is a critical factor. Their excellent mechanical properties, combined with good toughness and superior corrosion resistance, make titanium tubes indispensable in many industries.
Primarily, titanium tubes are utilized in the aerospace industry for manufacturing compressor components in aircraft engines. They also play a crucial role in constructing structural elements for rockets, missiles, and high-speed aircraft, where their strength-to-weight ratio offers significant advantages.
Beyond aerospace, the mid-1960s saw a surge in the use of titanium and its alloys in general industrial applications. They have been instrumental in creating electrodes for the electrolysis industry, condensers in power stations, heaters for petroleum refining, and equipment for seawater desalination processes. The ability of titanium to resist corrosion has made it an invaluable material in environmental pollution control devices, solidifying its status as a corrosion-resistant structural material.
Additionally, titanium alloys extend their utility to other advanced applications such as hydrogen storage materials, which are essential for energy storage and transportation, and shape memory alloys that are used in various smart systems and devices that rely on their unique ability to return to a predefined shape when subjected to heat.
In summary, the adaptability and robust characteristics of titanium tubes have made them a vital component across numerous sectors, from aerospace and general industry to emerging technologies that require materials with superior performance capabilities.