-
Titanium Pipe Fittings
-
Titanium Welded Pipe
-
Titanium Pipe Flange
-
Seamless Titanium Tubing
-
Titanium Heat Exchanger
-
Titanium Coil Tubing
-
Titanium Alloy Sheet
-
Titanium Fasteners
-
Titanium Welding Wire
-
Titanium Round Bar
-
Titanium Forgings
-
Titanium Clad Copper
-
Titanium Electrode
-
Metal Sputtering Target
-
Zirconium Products
-
Sintered Porous Filter
-
Shape Memory Nitinol Wire
-
Niobium Products
-
Tungsten Products
-
Molybdenum Products
-
Tantalum Products
-
Equipment Products
-
Aluminum Products
-
Stainless Steel Products
Titanium Anodes For Aluminum Foil Forming
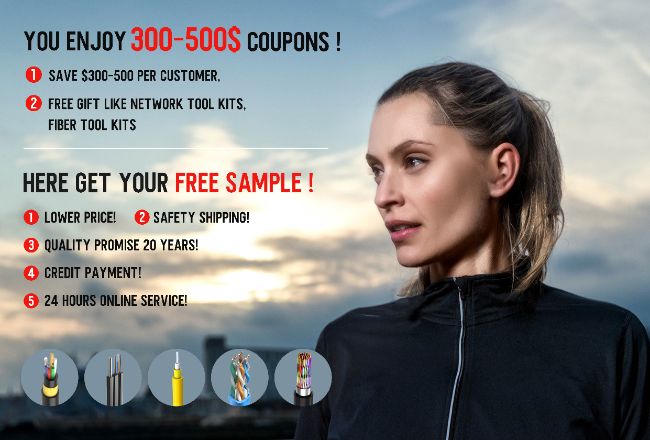
Contact me for free samples and coupons.
Whatsapp:0086 18588475571
Wechat: 0086 18588475571
Skype: sales10@aixton.com
If you have any concern, we provide 24-hour online help.
xPowder Or Not | Not Powder | Design Life | 9-18 Months |
---|---|---|---|
Current Density | 400-1000 ( A/sqm) | Diameter | Customized |
Coating | Titanium-based Iridium-Tantalum (Low Oxygen Evolution Overpotential) | Substrate | Titanium Gr1 Gr2 |
Highlight | Not Powder Titanium Anodes,EV Charging Station Titanium Anodes |
This titanium anode is specifically designed for the forming process of aluminum foil used in capacitors for EV charging stations. It features a long service life, stable dimensions, low working voltage, and excellent corrosion resistance. The anode ensures efficient and consistent oxide film formation, helping improve capacitor performance and energy efficiency in charging pile systems.
Application Background
In the electronics industry, the demand for high-purity anodized aluminum foil has increased significantly in recent years. To obtain a uniform oxide film with high capacitance, the aluminum foil must undergo a forming process in specially formulated electrolytes. Since it is difficult for current to pass directly through the thin aluminum foil, auxiliary anodes and cathodes must be installed on both sides of the foil to enable indirect current conduction.
In response to the specific needs of this industry, Changsheng Titanium has developed a specialized anode coating technology. With many years of technical experience, our company produces titanium anode plates for aluminum foil forming that offer long service life, excellent dimensional stability, low working voltage, and low energy consumption. During electrolysis, the electrode spacing remains constant, ensuring stable cell voltage and reliable forming conditions. These titanium anodes are capable of operating in highly corrosive or specialized electrolyte environments.
The titanium anode plates for aluminum foil forming developed by Changsheng Titanium have been widely applied in high-, medium-, and low-voltage aluminum foil forming production lines.
Production Process
Sandblasting
The substrate surface is treated with sandblasting to enhance its mechanical properties and improve durability. This process removes surface impurities, discoloration, and oxide layers, while increasing the total electrocatalytic surface area of the electrode plate to enhance catalytic efficiency.
Acid Pickling
The pickling solution typically consists of a mixture of various acids. It removes surface impurities and roughens the substrate surface to the greatest extent possible, thereby strengthening the bonding force between the substrate and the coating.
Brushing (Coating)
A prepared noble metal solution is evenly brushed onto the substrate and then dried. This allows the solution to bond quickly and uniformly with the base material.
Sintering
After drying, the anode plate is placed in a sintering furnace and held at a constant temperature for a specific period, then removed and allowed to cool naturally.
Quality Inspection
Final inspection ensures that all base dimensions are accurate. The coating surface is carefully examined for scratches, and adhesion strength tests are conducted to confirm product quality.
Packaging
After passing quality inspection, each shipment is packaged with a product test report, delivery note, certificate of conformity, and packing list.
Product Application
Operating Conditions: Ammonium adipate, Potassium adipate, Ammonium borate
Current Density: 400–1000 A/m²
Voltage: 25–26 V
Plate Dimensions: Customizable
Coating Type: Titanium-based Iridium-Tantalum (Low Oxygen Evolution Overpotential)
Service Life: 9–18 months
Electrochemical Performance & Service Life Testing: According to standards HG/T 2471-2007 and Q/CLTN-2012