-
Titanium Pipe Fittings
-
Titanium Welded Pipe
-
Titanium Pipe Flange
-
Seamless Titanium Tubing
-
Titanium Heat Exchanger
-
Titanium Coil Tubing
-
Titanium Alloy Sheet
-
Titanium Fasteners
-
Titanium Welding Wire
-
Titanium Round Bar
-
Titanium Forgings
-
Titanium Clad Copper
-
Titanium Electrode
-
Metal Sputtering Target
-
Zirconium Products
-
Sintered Porous Filter
-
Shape Memory Nitinol Wire
-
Niobium Products
-
Tungsten Products
-
Molybdenum Products
-
Tantalum Products
-
Equipment Products
-
Aluminum Products
-
Stainless Steel Products
Coil Titanium Shell And Tube Heat Exchanger For Seawater Desalination
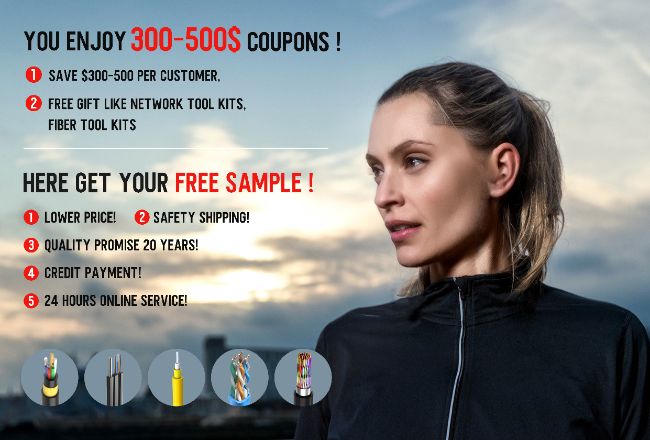
Contact me for free samples and coupons.
Whatsapp:0086 18588475571
Wechat: 0086 18588475571
Skype: sales10@aixton.com
If you have any concern, we provide 24-hour online help.
xMain Materials | Grade 2 Titanium Purity: >99.8% | Shape | Fixed Tube-sheet Exchanger |
---|---|---|---|
Pressure | No | Attributes | Best Corrosion Resistance To Chlorine Chemicals |
Dimension | 1.2*3.5M | Thickness | 10mm |
Weight | 1.3 Tons | ||
Highlight | Titanium Shell And Tube Heat Exchanger,Full Titanium Coil Heat Exchanger,Fixed Shell And Tube Heat Exchanger |
Full Titanium Shell Tube Tubular Heat Exchanger
Specifications:
Material of Tube Pass: | Gr1, Gr2, TA1, TA2 |
Material of Shell: | Gr1, Gr2, TA1, TA2 |
Other Parts: | Tube sheet, tube box, baffle, head |
Titanium Purity | >99.8% |
Heat Exchange Area: | 100-1000M2 |
Size: |
Dia.1-10m Length: 2m-14m Design according to customer's requirements, or process according to drawing requirements |
Delivery time: | 1-3 months |
Factors to Consider When Designing Titanium Heat Exchangers:
Shell and tube heat exchangers consist of a series of tubes. One set of these tubes contains the fluid that must be either heated or cooled. The second fluid runs over the tubes that are being heated or cooled so that it can either provide the heat or absorb the heat required. A set of tubes is called the tube bundle and can be made up of several types of tubes: plain, longitudinally finned, etc. Shell and tube heat exchangers are typically used for high-pressure applications (with pressures greater than 30 bar and temperatures greater than 260°C). This is because the shell and tube heat exchangers are robust due to their shape.
There are several thermal design features that are to be taken into account when designing the tubes in the shell and tube heat exchangers. These include:
1. Tube diameter: Using a small tube diameter makes the heat exchanger both economical and compact. However, it is more likely for the heat exchanger to foul up faster and the small size makes mechanical cleaning of the fouling difficult.
To prevail over the fouling and cleaning problems, larger tube diameters can be used. Thus to determine the tube diameter, the available space, cost and the fouling nature of the fluids must be considered.
2. Tube thickness: The thickness of the wall of the tubes is usually determined to ensure:
- There is enough room for corrosion
- That flow-induced vibration has resistance
- Axial strength
- Availability of spare parts
- Hoop strength (to withstand internal tube pressure)
- Buckling strength (to withstand overpressure in the shell)
3. Tube length: heat exchangers are usually cheaper when they have a smaller shell diameter and a long tube length. Thus, typically there is an aim to make the heat exchanger as long as physically possible whilst not exceeding production capabilities. However, there are many limitations for this, including the space available at the site where it is going to be used and the need to ensure that there are tubes available in lengths that are twice the required length (so that the tubes can be withdrawn and replaced). Also, it has to be remembered that long, thin tubes are difficult to take out and replace.
4. Tube pitch: when designing the tubes, it is practical to ensure that the tube pitch (i.e., the centre-centre distance of adjoining tubes) is not less than 1.25 times the tubes' outside diameter. A larger tube pitch leads to a larger overall shell diameter which leads to a more expensive heat exchanger.
5. Tube corrugation: this type of tubes, mainly used for the inner tubes, increases the turbulence of the fluids and the effect is very important in the heat transfer giving a better performance.
6. Tube Layout: refers to how tubes are positioned within the shell. There are four main types of tube layout, which are, triangular (30°), rotated triangular (60°), square (90°) and rotated square (45°). The triangular patterns are employed to give greater heat transfer as they force the fluid to flow in a more turbulent fashion around the piping. Square patterns are employed where high fouling is experienced and cleaning is more regular.
7. Baffle Design: baffles are used in shell and tube heat exchangers to direct fluid across the tube bundle. They run perpendicularly to the shell and hold the bundle, preventing the tubes from sagging over a long length. They can also prevent the tubes from vibrating. The most common type of baffle is the segmental baffle. The semicircular segmental baffles are oriented at 180 degrees to the adjacent baffles forcing the fluid to flow upward and downwards between the tube bundle. Baffle spacing is of large thermodynamic concern when designing shell and tube heat exchangers. Baffles must be spaced with consideration for the conversion of pressure drop and heat transfer. For thermo economic optimization it is suggested that the baffles be spaced no closer than 20% of the shell’s inner diameter. Having baffles spaced too closely causes a greater pressure drop because of flow redirection. Consequently having the baffles spaced too far apart means that there may be cooler spots in the corners between baffles. It is also important to ensure the baffles are spaced close enough that the tubes do not sag. The other main type of baffle is the disc and donut baffle which consists of two concentric baffles, the outer wider baffle looks like a donut, whilst the inner baffle is shaped as a disk. This type of baffle forces the fluid to pass around each side of the disk then through the donut baffle generating a different type of fluid flow.
Features:
- Developed with advanced technology.
- Energy saving.
- High efficiency.
- Anti-corrosion.
- Long service life.
- Low cost.
Application:
Seawater, Oil, Food, Distilled Water, Gas industries.
Titanium Fabrications:
In 1975, our engineers entered the titanium industry and followed the earliest group of titanium experts and engineers in China to study, develop and practice the application of titanium. In 2001, Changsheng Titanium Enterprice was established to manufacture titanium equipment. We support structural design, manufacturing and installation guidance
- Titanium Heat Exchangers
- Titanium Columns
- Titanium Condensers
- Titanium Reactors
- Titanium Pressure Vessels
- Titanium Piping Systems
- Titanium Pipe Fittings